Common Challenges and Troubleshooting Tips for Hydraulic Cold Press Machines
- Surekha Sarode
- May 26, 2023
- 2 min read
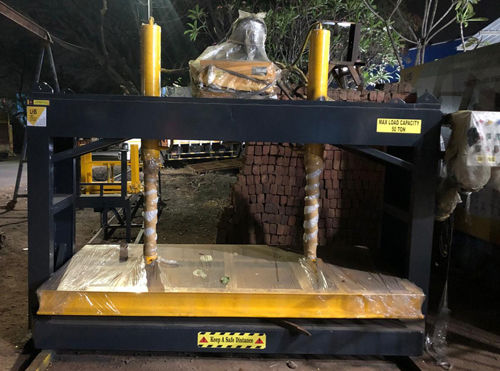
Hydraulic cold press machines are essential equipment in the woodworking industry, offering efficient and precise pressing of materials. However, like any mechanical system, they can encounter challenges that may hinder their performance. In this blog, we will explore some common challenges faced by hydraulic cold press machines and provide practical troubleshooting tips to overcome them. By understanding these issues and implementing the suggested solutions, operators can optimize the functionality of their machines and ensure smooth operations.
Insufficient Pressure:
One common challenge is insufficient pressure during the pressing process. This can result in incomplete bonding or inadequate compression. To troubleshoot this issue:
Check the hydraulic system for any leaks or damaged hoses.
Inspect the hydraulic pump and valves for proper operation.
Verify that the pressure gauge is functioning accurately.
Ensure that the machine is receiving sufficient power supply.
Slow Pressing Cycle:
If the pressing cycle is excessively slow, it can impact productivity. Here are some troubleshooting steps to address this challenge:
Examine the hydraulic fluid level and quality. Replace or refill the fluid if necessary.
Inspect the hydraulic pump for any issues, such as worn-out components or low oil pressure.
Check the system's pressure relief valve to ensure it is not excessively restricting flow.
Clean or replace clogged filters and strainers in the hydraulic system.
Verify that the press platen and workpiece are properly aligned to prevent unnecessary friction.
Excessive Noise and Vibration:
Unusual noise and excessive vibration can indicate underlying problems. To troubleshoot this challenge:
Inspect the hydraulic system for loose or damaged components, such as bolts, nuts, or brackets.
Check the hydraulic pump and motor for misalignment or worn-out bearings.
Lubricate moving parts and ensure they are properly greased.
Evaluate the condition of the hydraulic fluid and replace it if contaminated.
Verify that the press is properly balanced and leveled to minimize vibration.
Inconsistent Pressing R
results:
If the pressing results vary or are inconsistent, it can affect the quality of the final product. Here are some troubleshooting tips:
Verify that the pressure gauge is accurate and calibrated correctly.
Inspect the press plates for any warping or damage that may affect uniform pressure distribution.
Ensure that the workpiece is properly positioned and aligned on the press bed.
Check the temperature and humidity levels in the press environment, as they can affect the material's behavior.
Evaluate the press time and pressure settings, adjusting them as needed for different materials and thicknesses.
Hydraulic Fluid Leaks:
Leaks in the hydraulic system can lead to a loss of pressure and potential damage to the machine. Here's how to troubleshoot this challenge:
Inspect all hydraulic hoses, fittings, and connections for leaks or damage. Replace or repair as necessary.
Check the hydraulic cylinder seals
for wear or degradation and replace them if needed.
Ensure that the hydraulic reservoir is properly sealed and that the fluid level is within the recommended range.
Clean and tighten all connections to prevent any potential leaks.
Comentarios